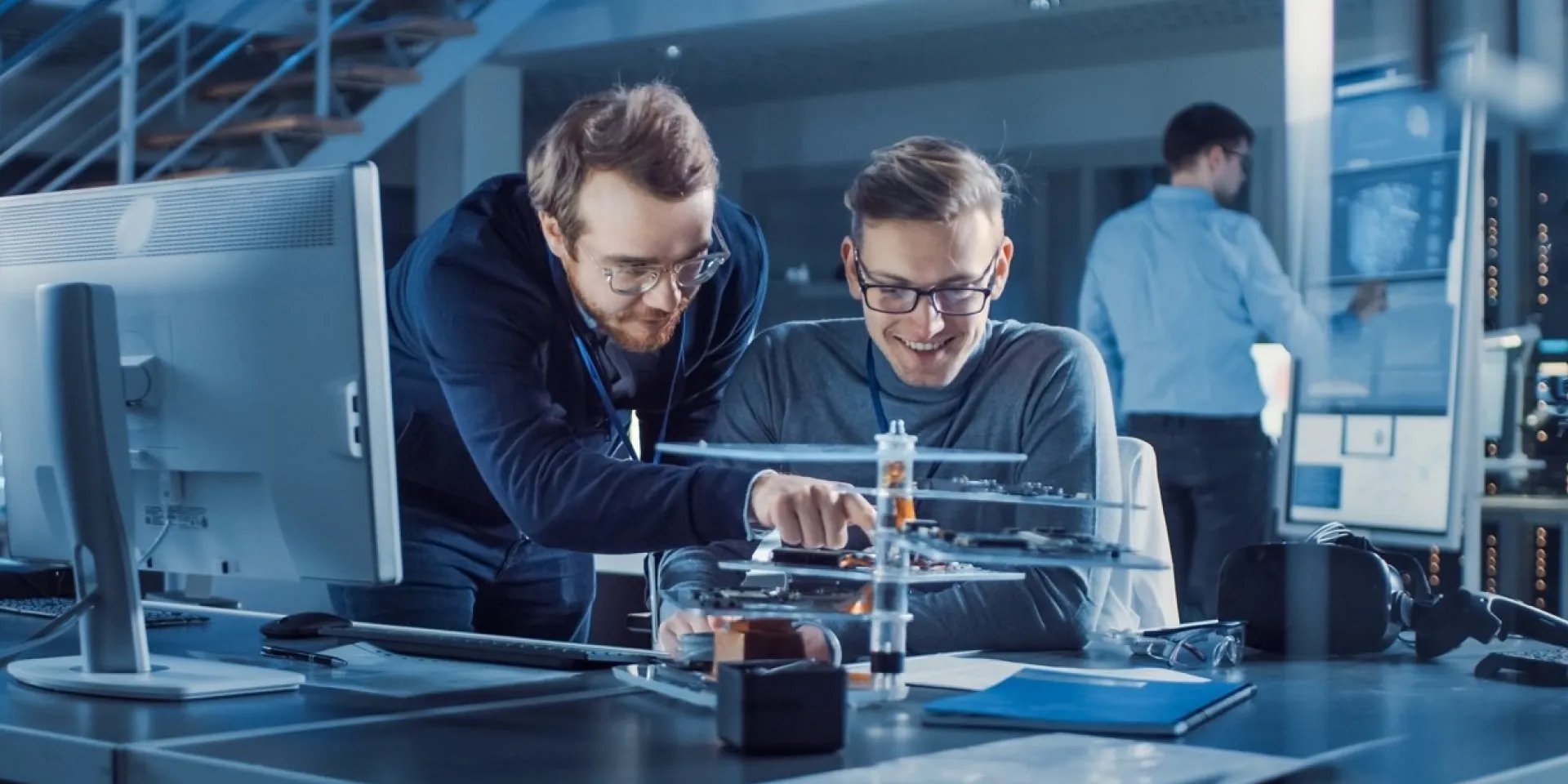
Product Engineer
A Product Engineer is a professional responsible for the design, development, and manufacturing of products. They play a critical role in translating design concepts into practical, functional, and manufacturable products. Product Engineers work in a wide range of industries, including consumer electronics, automotive, aerospace, medical devices, and more. Their role is crucial in bringing innovative and functional products to market, from initial concept to final production. They bridge the gap between design and manufacturing, ensuring that products are not only aesthetically appealing but also feasible to manufacture and meet quality standards.
Product Design: Collaborating with design teams to develop product concepts and specifications that meet customer needs and market requirements. Managing timelines, milestones, and budgets to ensure that the product development process stays on track.
Design Validation: Conducting feasibility studies and simulations to validate the design's functionality, performance, and manufacturability.
Prototyping: Creating prototypes or mock-ups of the product to test and refine design concepts before full-scale manufacturing. Considering user needs, ergonomics, and usability to create products that offer a positive user experience.
Material Selection: Selecting appropriate materials for the product based on factors such as durability, cost, and performance requirements.
Manufacturability: Designing products for efficient and cost-effective manufacturing processes, considering factors like assembly, machining, molding, and fabrication. Collaborating with suppliers to source components, materials, and parts required for product manufacturing.
CAD Modeling: Creating detailed 3D models and technical drawings using Computer-Aided Design (CAD) software.
Testing and Quality Control: Developing testing procedures and quality control measures to ensure the product meets specifications and standards.
Continuous Improvement: Identifying opportunities for design enhancements, cost reduction, and performance optimization through continuous improvement initiatives. Addressing design challenges and issues that arise during the development and manufacturing phases.
Documentation: Creating detailed technical documentation, specifications, and assembly instructions for manufacturing and quality control.
keys Roles and Responsibility
Software Skills
3DCS - GD&T , Tolerance stack ups and Dimensional Variation Analysis
Autodesk Inventor - Expert in Mechanical Design
Creo - Expert in Mechanical Design
NX - Expert in Mechanical Design
Solidworks - Expert in Mechanical Design
Solidworks - Expert in Simulation
ANSYS Mechanical - Getting Started
MathCAD - Engineering Analysis Approach
Matlab - Engineering Analysis Approach
Technical Skills
ASME - Y14.5 Geometric Dimensioning and Tolerancing (GD&T)
Design For Manufacturability and Assembly (DFM/DFA)
Design for the Six Sigma
Fundamental of New Product Development
Fundamental of New Product Introduction
Fundamentals of Failure Modes and Effects Analysis
Fundamentals of 8D Problem Solving
Fundamentals of Weibull Analysis and Design of Experiment
Fundamentals of Root Cause Analysis
Introduction to Advanced Product Quality Planning (APQP)
Introduction to Continuous Improvement Management
Certification
Lean Six Sigma Green Belt - ASQ
Lean Six Sigma Green Belt - IASSC
How to become PMI Project Management Professional?