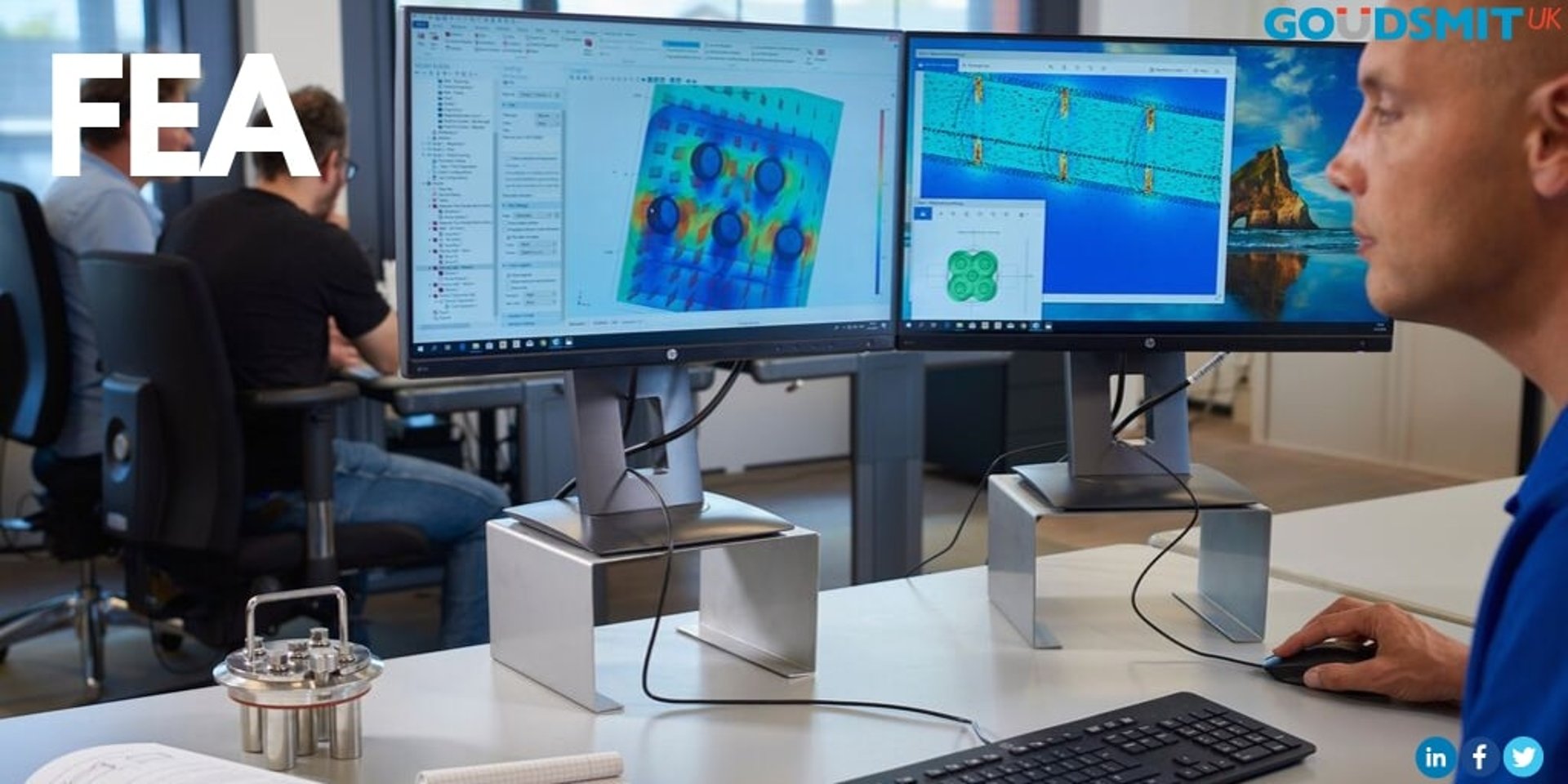
FEA Engineer
An FEA (Finite Element Analysis) engineer is responsible for utilizing the finite element method, a numerical technique, to simulate and analyze the behavior of complex structures and systems under various conditions. FEA engineers play a critical role in various industries, including aerospace, automotive, civil engineering, and more.
Model Creation: FEA engineers create detailed computer models of structures or systems using specialized software. They break down the geometry into smaller elements (finite elements) to approximate the behavior of the real structure. These models include information about materials, loads, boundary conditions, and other relevant parameters.
Material Properties: They input accurate material properties into the model. Different materials exhibit different behaviors under stress, temperature changes, and other factors, so accurate material data is essential for accurate simulations.
Meshing: FEA engineers divide the geometry into finite elements through a process called meshing. Proper meshing is crucial for accurate results; it involves determining how finely the structure should be divided for accurate analysis without overwhelming computational resources.
Boundary Conditions: Engineers apply boundary conditions to represent the constraints and loads that the real structure would experience. These conditions include fixed points, forces, moments, and thermal effects.
Solving Equations: The FEA software sets up and solves a system of equations based on the finite element model. This simulation calculates how the structure responds to the applied loads and constraints, providing insights into stress distribution, deformation, and other behaviors.
Interpreting Results: FEA engineers analyze the simulation results to understand how the structure behaves under different conditions. They assess factors like stress concentration areas, deformation, stability, and failure points.
Optimization: Engineers may use FEA to optimize designs by iterating through different configurations to find the most efficient and safe solution. This might involve altering geometries, materials, or load distributions.
Validation: Engineers compare FEA results with physical tests to validate the accuracy of their simulations. This helps build confidence in the FEA model's predictions.
Collaboration: FEA engineers often collaborate with other engineers and designers to improve designs and solve structural problems. They might work with CAD (Computer-Aided Design) professionals, material specialists, and others to ensure the overall success of a project.
keys Roles and Responsibility
Software Skills
Abaqus - Composite Modeling
Abaqus - Getting Started with Linear and Nonlinear Analysis
Altair HyperWorks – Learn the Basics
Altair Inspire - Learn Conceptual Design
Altair Inspire - Learn the Basic of Manufacturing Simulation
Altair MotionView and MotionSolve - Learn the Basics of MBS
Altair OptiStruct - Learn Composite Optimization
Altair OptiStruct - Learn Lattice and Multi Model Optimization
Altair OptiStruct - Learn Optimization Fundamentals
Altair OptiStruct - Learn Shape and Free Shape Optimization
Altair OptiStruct - Learn Size and Free Size Optimization
Altair OptiStruct - Learn the Basics of Composite Analysis
Altair OptiStruct - Learn the Basics of Fatigue Analysis
Altair OptiStruct - Learn the Basics of Linear Dynamics
Altair OptiStruct - Learn the Basics of Nonlinear Analysis
Altair OptiStruct - Learn the Basics of Thermal Analysis
Altair OptiStruct - Learn Topography Optimization
Altair OptiStruct - Learn Topology Optimization
Altair Radioss - Learn the Basics of Explicit Analysis
ANSYS - Explicit Dynamics
ANSYS - Introduction to ACT Wizards
ANSYS Fluent - Aeroacoustics
ANSYS Fluent - Combustion Modeling
ANSYS Mechanical - Acoustics
ANSYS Mechanical - Basic Structural Nonlinearities
ANSYS Mechanical - Beam and Shell Modeling
ANSYS Mechanical - Beyond the Basic
ANSYS Mechanical - Commands Objects
ANSYS Mechanical - Fatigue
ANSYS Mechanical - Fracture Mechanics
ANSYS Mechanical - Heat Transfer
ANSYS Mechanical - Introduction to APDL
ANSYS Mechanical - Introduction to nCode DesignLife
ANSYS Mechanical - Linear and Non-Linear Dynamics
ANSYS Mechanical - Material Nonlinearities
ANSYS Mechanical - Rigid Body Dynamics
ANSYS Mechanical - Rotodynamic
ANSYS Mechanical - Scripting
Comsol - Getting Started Acoustics
Comsol - Getting Started Chemical Engineering
Comsol - Getting Started Geomechanics
Comsol - Getting Started Multibody Dynamics
Comsol - Getting Started Structural Mechanics
Foundation of FEA Modeling with Simcenter Femap
Advanced Simcenter Femap
MSC Actran - Introduction to Vibration and Acoustics
MSC Apex - Getting Started
MSC Marc and Mental - Basic of Non-linear Analysis
MSC Marc and Patran - Basic of Non-linear Analysis
MSC Nastran - Aeroelasticity Analysis
MSC Nastran - Composite Material Analysis
MSC Nastran - Dynamic Analysis
MSC Nastran - Explicit and Implicit Nonlinear Analysis
MSC Nastran - Getting Started with Linear Analysis
MSC Nastran - Implementation of Fatigue Methods
MSC Nastran - Rotodynamic Analysis
MSC Patran - Aeroelasticity Analysis
MSC Patran - Composite Material Analysis
MSC Patran - Durability and Fatigue Life Analysis
MSC Patran - Getting Started
MSC Patran - GUI Customization and Automation using the Patran Programming Command Language