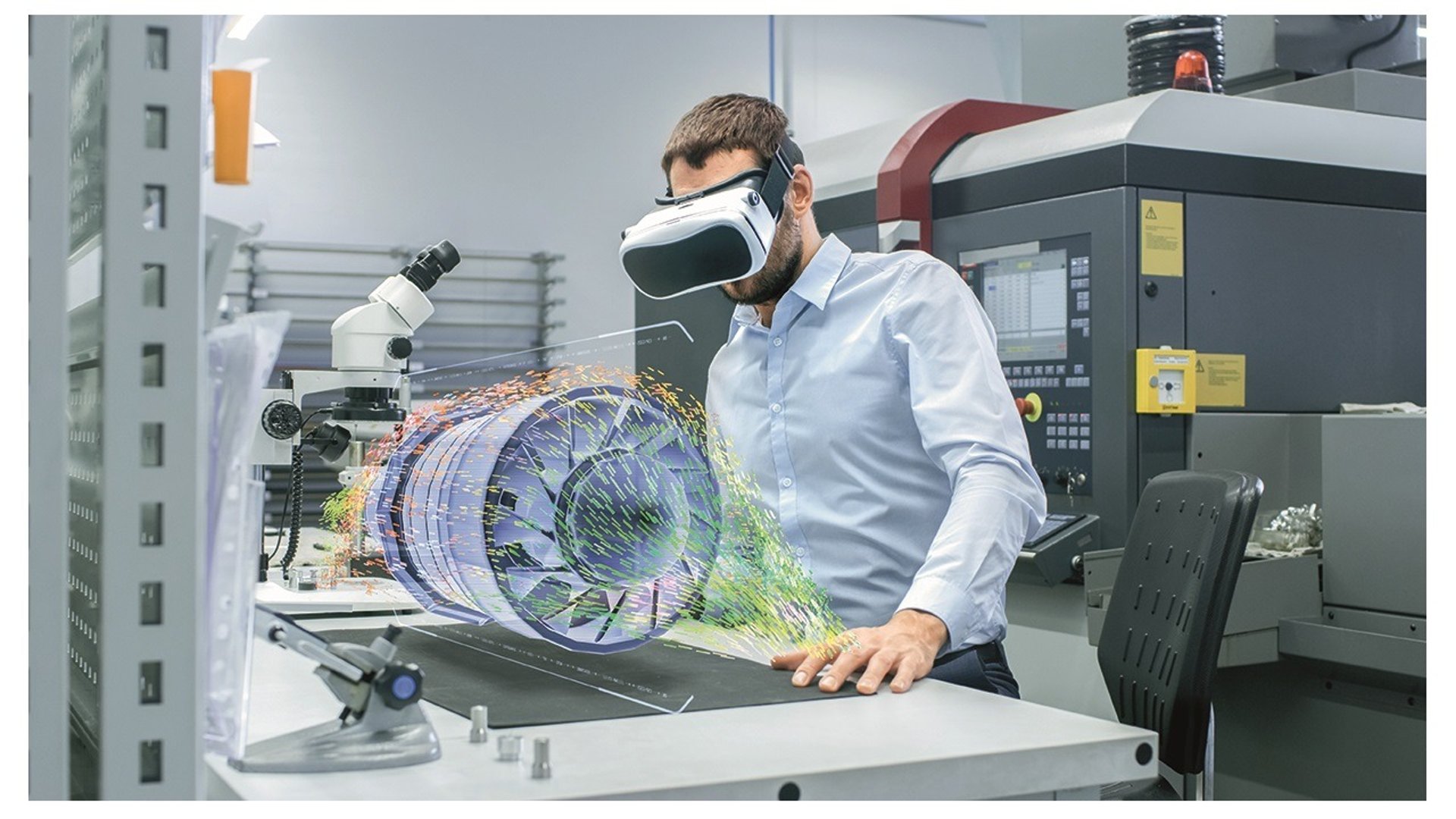
CFD Engineer
A Computational Fluid Dynamics (CFD) engineer is responsible for utilizing numerical simulations to analyze the behavior of fluid flows and their interactions with solid structures. CFD engineers play a crucial role in various industries, including aerospace, automotive, energy, environmental science, and more.
Model Creation: CFD engineers create computer models that represent the geometry of the fluid domain and any solid objects within it. The model includes information about the fluid properties, boundary conditions, and other relevant parameters.
Mesh Generation: Similar to FEA, CFD engineers divide the fluid domain into smaller computational cells or elements through meshing. The quality of the mesh affects the accuracy and efficiency of the simulation.
Boundary Conditions: Engineers define the conditions at the boundaries of the fluid domain, including inflow velocities, outflow pressures, and no-slip conditions on solid surfaces. These conditions determine how fluid interacts with the boundaries.
Equation Solving: CFD software solves the governing equations of fluid dynamics, including the Navier-Stokes equations that describe the behavior of fluids. These equations are solved numerically for each cell in the mesh to simulate the flow behavior.
Turbulence Modeling: In cases where the flow becomes turbulent, CFD engineers use various turbulence models to simulate the complex behavior of turbulence, which is critical for understanding real-world flows.
Heat Transfer: CFD can also simulate heat transfer processes like conduction, convection, and radiation. CFD engineers can analyze how temperature gradients affect fluid flow patterns and heat distribution.
Pressure and Velocity Distribution: CFD engineers analyze the resulting pressure, velocity, and temperature distributions within the fluid domain. They can identify areas of low pressure (vacuum), high-pressure regions, and flow separation zones.
Aerodynamics and Hydrodynamics: In aerospace and automotive industries, CFD engineers study the aerodynamics of aircraft, cars, and other vehicles to optimize their design for better performance, fuel efficiency, and stability. In maritime industries, they analyze hydrodynamics for ships and underwater vehicles.
Optimization: CFD simulations can help engineers optimize designs by iterating through different configurations to find the most efficient and aerodynamically effective solution.
keys Roles and Responsibility
Software Skills
Altair Acusolve - Learn the Basic of Computation Fluid Dynamics
ANSYS CFX - Fluid Structure Interaction
ANSYS CFX - Multiphase Flow Modeling
ANSYS CFX - Rotating Machinery
ANSYS Fluent - Advanced Meshing
ANSYS Fluent - Aeroacoustics
ANSYS Fluent - Combustion Modeling
ANSYS Fluent - External Aerodynamics
ANSYS Fluent - Fluid Structure Interaction
ANSYS Fluent - Meshing with Fault-Tolerant Meshing (FTM) Workflow
ANSYS Fluent - Meshing with Watertight Geometry Workflow
ANSYS Fluent - Multiphase Flow Modeling
ANSYS Fluent - Rotating Machinery Modeling
Comsol - Getting Started Fluid Flow
Simulia Xflow - Getting Started
MSC Nastran - Fluid Structure Analysis
MSC Cradle - Getting Started
OpenFoam - Getting Started
OpenFoam - Intermediate
SIEMENS FLOEFD - Getting Started with Computational Fluid Dynamics Simulation
SIEMENS STAR-CCM+ - Getting Started with Computational Fluid Dynamics Simulation
Solidworks - Expert in Flow Simulation